And so the saga continues with ownership of BMW's wonderfully designed rear axle carrier panel that just can't quite hold the power of M. I guess owning a car that tries to kill itself with every drive out is a cool statement but we all know there is a much larger fault that most don't know about!
The goal was to install Vincebar (which I have in my hands now) with epoxy and rivets to distribute load across a far greater and stronger area compared to just plates as over time the new cracks form on the RACP around the plates. The load of the subframe/engine/driveshaft twist is not modified via just plates so the next weakest point will fail. That's why I decided to trust Vince who is a mechanical engineer and based out of Sweden after he showed his solution to finally fix the E46 chassis rather than "prolong" damage.
Vince's system is quite amazing and installing only requires just lowering the subframe but not completely removing it. Except as my subframe was lowered, the nightmare of many had become my reality. It was time to begin the lengthy process to fully drop the subframe.
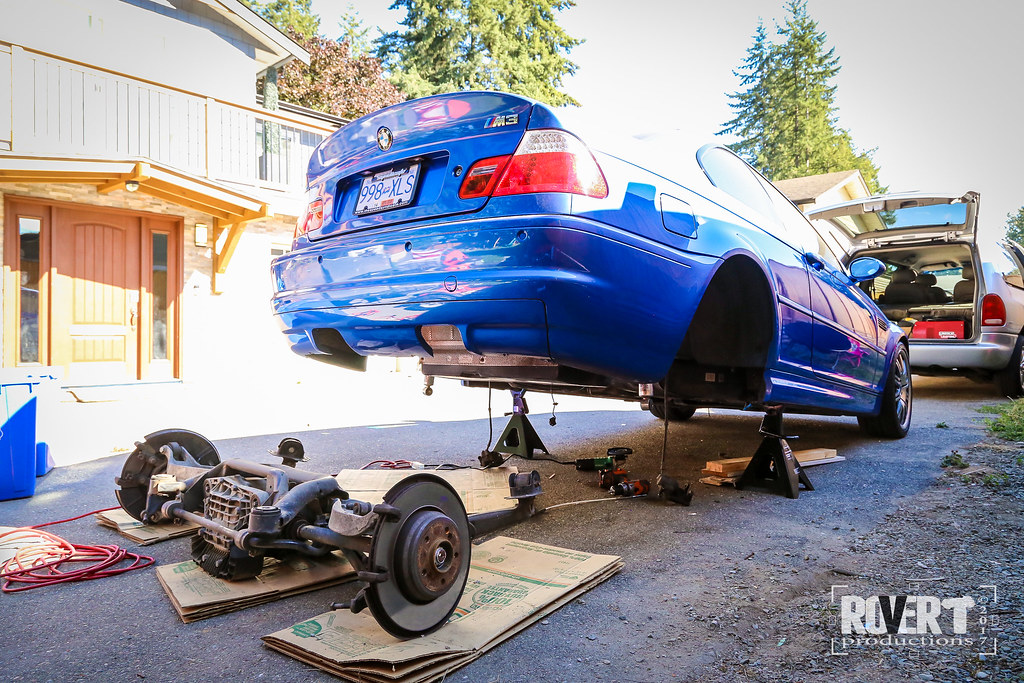
Subframe and Body RACP-5443
You can see the front right RACP mount isn't looking too hot:

Front RACP
Just a bit devastating...
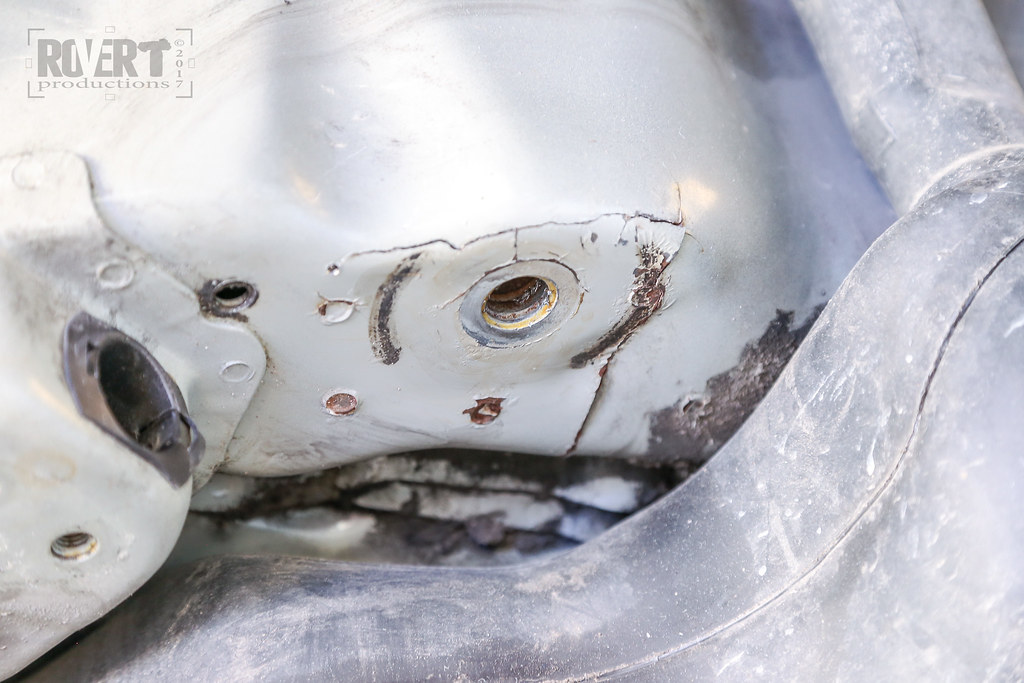
Front Right RACP
What I learned is that the subframe truly needs to be dropped to fully inspect as the size of the bushing can hide most if not ALL of the RACP failure in that area.
Now for the front left, which shows failure beginning...
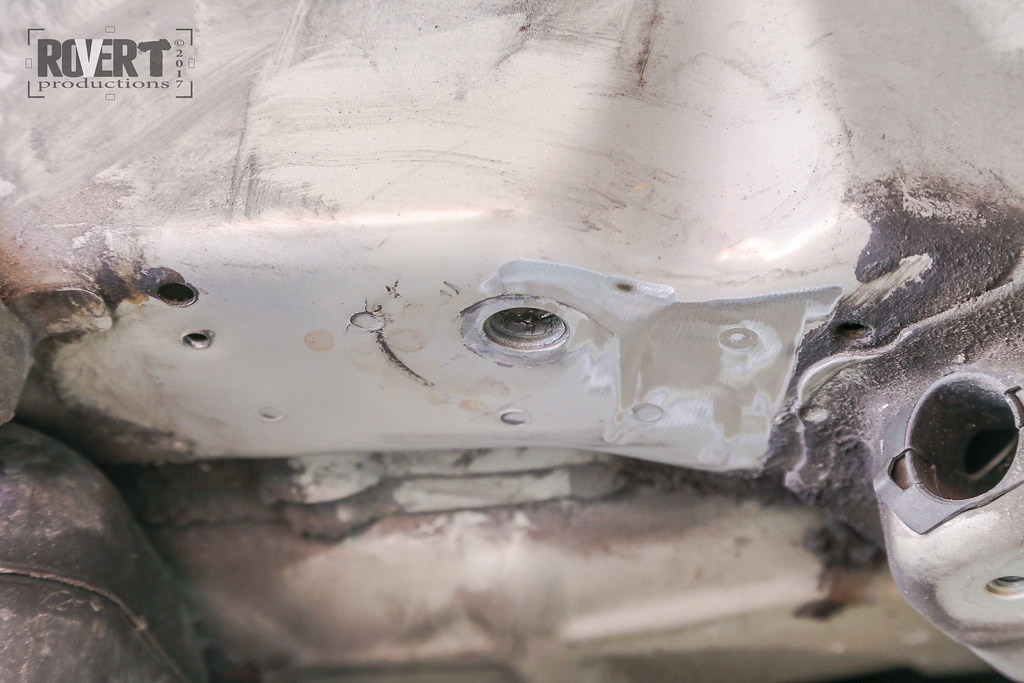
Front Left RACP
The rear right is showing the cleanest of corners but still signs of failure are happening...
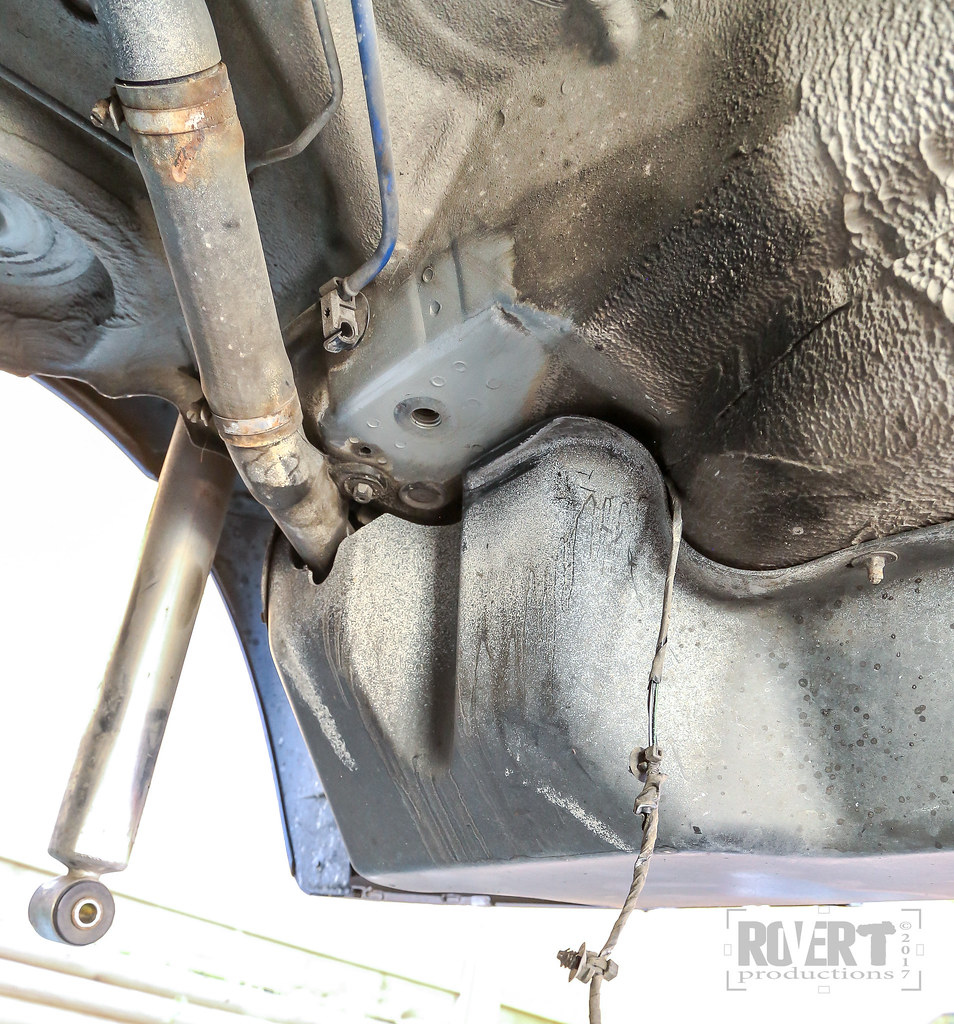
Rear Right RACP
And now onto the left corner, the rear left...
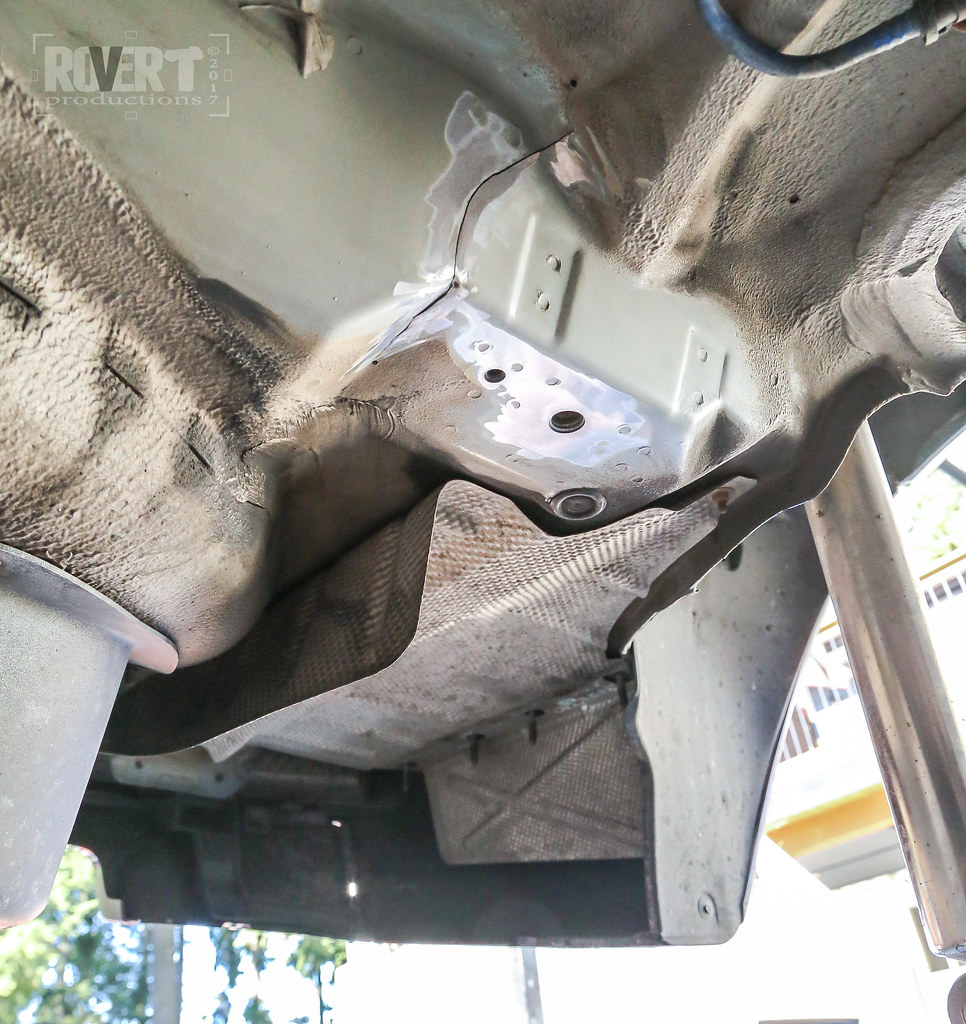
Rear Left RACP
This doesn't look good. It's weird that even under inspections you couldn't see this.

Rear Left RACP
Thanks to Vince and the wonder of technology, he has studied my pictures and given me so much more information on this subject. He is also taking the time to fabricate some of the first Vinceskinz to epoxy/rivet into my car because it's in the air and there is an urgency to address and fix the situation ASAP. These "skinz" are like Reddish plates but they mold very tightly to the curvature of the RACP mounts from stage 1 to stage 4. The highest stage meaning more coverage due to more serious/lengthy cracking.
During all of this, I asked Vince questions for more clarity.
Why Epoxy and rivet your product instead of weld?
"Epoxy will adhere the complete surfaces to each other, completely embedding the cracks. The rivets will not only clamp the skins to the RACP while the epoxy cures, but they will also tie the skins to the base plate, and other underlying multilayer parts of the RACP. The placement of the rivets is very thoroughly researched.
Given the complex shape the skins are snuggly following, I really don't see that being possible without the rivets (think aerospace applications). The gaps would be too large which makes for a weak bond (which is most likely the issue for people who haven't really succeeded with epoxy installations). Even though I've made the Skinz fit very tightly.
But if you're concerned about epoxying you could try welding them on. Just add a lot more small holes in which you could add plug welds. Otherwise, the Skinz will only be a thin plate slapped on top the RACP."
Another question I ask was about spot welding and this was his response:
"Yes, spot welding a little at a time is typically what needs to be done in order to weld that thin sheet metal with gaps.
But it's not the warping you should be concerned about, it's the local heat in the spot weld weakening the metal. So the welded crack will not be as strong as before. And the crack is in that specific location because it's a high load area.
That's why I argue you should cover the cracked area with a skin that is epoxied on. Which will effectively make that area, and a large area around it stronger.
But yes, the VinceBar Kit does provide a significant load relief. So the cracked areas will not see stress anywhere near what they originally were subject to. So just welding could work. I just feel it's a bit of a gamble, and fabricating and fitting plates to fit snuggly is a lot more difficult and time consuming than you would think."
When he brought up skinz for my car I asked him why use those over other "plates"?
"Well, it's about covering the correct area and doing so while being smart about material usage.
Slapping on thick plates will create stress concentrations at the perimeters of those thick plates (a large step in thickness), and that's also where they are welded, and the welding weakens the metal...
Epoxied and riveted VinceSkinz are uniformly connected to the whole coverage surface making it a thickening process so to say, rather than a plate transferring load. Without weakening the metal by welding.
Also, those plates leave much of the cracked area uncovered because it's difficult and time consuming to make plates cover those areas. So they simply drop that for cost reasons.
Plates are not about transferring load, the load should be taken care of with the load relief solution. The plates/skins are about efficiently and smartly repair and reinforce weak areas of the RACP. To better take the local loads.
The VinceSkinz are also very easy to install as they are already formed to follow the RACP. No hammering (that still doesn't provide coverage) is needed.
And the VinceSkinz are so far the only commercially available "plates" that do not require welding."
So I am getting schooled on how this all works and I'm excited that I will have a really buttoned down (or riveted down) mount for the subframe within the next two weeks. There are a lot of fine details to work out but I am getting great guidance from Vince and my buddy Josh who has agreed to be one of the first installers of this system. As I get more information I'll relay my findings to this thread since I believe this information will better arm all of you for the future.